Advantages of the directional drilling technique
- Quick: A modern drill can drill up to 100m in magnitude in a day.
- Precise: Modern measurement methods allow for precision as close as 10 cm.
- Comfortable: In contrast to other technologies where the pavement surface needs milling, drilling saves residents from traffic and noise caused by machinery and trucks, from long-term closure of the area and traffic jams, and helps prevent nuisances arising from other methods. In an area where directional drilling is applied, normal life never stops.
- Durable: No need to worry about subsequent surface damages or sinkage.
- Eco-friendly: Nature, as opposed to the milled area, suffers only point-like impacts, minimizing disturbances in the order of the environment. Contrary to open-trench technology, the original vegetation and soil surface remains undisturbed.
- Directional: In contrast to other technologies that do not use surface milling, directional drilling can be controlled depending on the inflection radius of the drill shank and the soil structure.
- Cost effective: There is no substantial soilwork and expensive remediation involved; neither is there traffic from machinery, hardly any waste is produced, no need for supporting services or complicated road blocks and traffic regulation methods… Moreover, the client is exempt right from the start from these expenses, not to mention the working hours involved.
Take a look at how the Zolmat Team works!
What is directional drilling?
Directional drilling is one of the most versatile technologies for laying down pipes without milling, and is a diversified solution in public utility construction.
The essence of the method is to create the passage from the surface, without digging a working trench, then expand it to the desired diameter and insert the product pipe from the outgoing access point.
The drilling itself is performed with a drill controlled from the surface via the rotation and injection of the drill shanks.
A radiosonde in the drill bit sends data about the actual direction and depth to the surface, whereby spatial positioning is calculated.
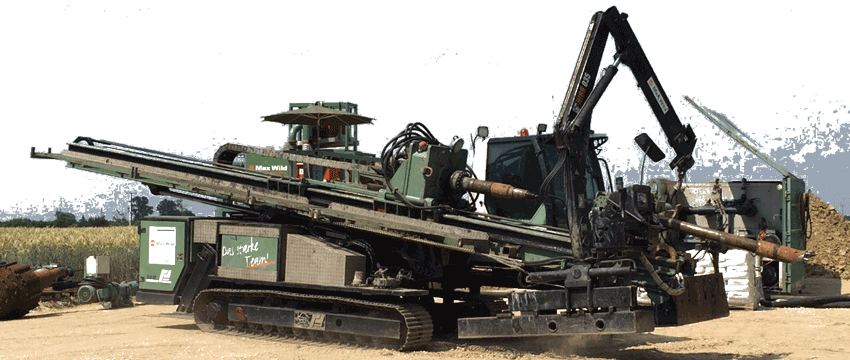
See more about our technologies under “No-Dig” digging
Horizontal directional drilling
This technology allows the underground installation of pipes under various objects (e.g., motorways, rivers, railway lines).
More ...Pipe jacking with a rocket drill
Condensed air forces the rocket piston, attached to the front of the utility pipe, to follow an alternating motion to exert impact toughness on the chisel head in the nose of the equipment, ensuring progress while extruding soil.
More ...Pipe jacking with a rammer
The steel pipe to be installed is driven through by a unique pipe driver equipment (rammer) under the facility that needs to be crossed (road, railway, stream, public utility, etc.)
More ..."There is practically not a single square mile within Hungary where we have not done work in the last 25 years."

FACTS
The Zolmat Team has completed 4.3 drills per day on average in 2015, including Sundays and holidays.
60% of our colleagues have been on the team for more than 10 years.